Experience Sharing
Successful Case of Center Material Handling System
This corporation in a development zone of
Harbin in
The corporation now is mainly producing
modified universal plastics, modified engineering plastics, alloy plastics and
environmental friendly plastics. It will gradually develop new products of high
adding value, like modified Bioplastics, and special engineering plastics in
the future. More than 90% of its products are applied into interior decorating
pieces, exterior decorating pieces, and functional pieces of more than 30 car
types of Audi, Hongqi, etc. It is the biggest manufacture of exclusive automotive
modified plastics in
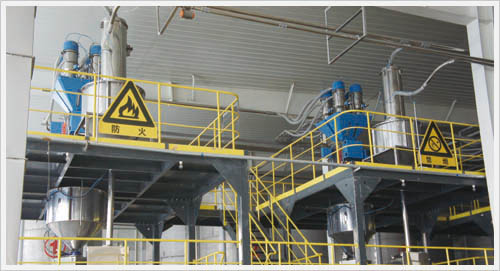
The corporation completed their plant in 2012.
It decided to introduce Shini central feeding system to further improving
plant’s image and individual management.
After confirming the final solution is practical, Shini sent designers
to examine on the spot to verify and get some related data, to understand
details of requirement of clients. Then, Shini made a 3D working drawing of 1:1
according to conditions on the ground, data and clients’ requirements. Under
supervision of supervising personnel appointed by clients, the whole project has
been successfully completed according to the working drawing. The whole project
from plan to construct is of science. Its system configuration is set out from
multi-angle and its construction is rigorous and scientific. This project not
only helps clients save cost and shorten time of putting the equipment into
production but also lay a sound foundation of creating a good image of Shini by
increasing efficiency of construction and saving construction cost.
The plan of system involves both conveying ways
of positive pressure and negative pressure. Nine siloes of 200T outside the
plant adopts conveying way of positive pressure while mixing and loading inside
the plant uses the negative one.
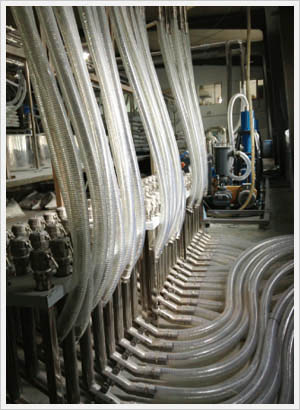
About raw materials, the machine material is
made of granule, recycled materials, talcum powder, and polypropylene powder.
Using the roots blower which has higher and more air pressure and volume, raw
materials are conveyed to gravimetric blender which guarantees products’
quality while mixing materials. Then raw materials are sent to machine
production lines by distribution station. It realizes the aim of more
accurately, more speedily, and more effectively conveying as well as
successfully meets clients’ requirements of centralized mixing and conveying.
Basing on analysis of the whole system’s operation performance, it can work
smoothly with no blocking of materials if required volume of materials is met
within
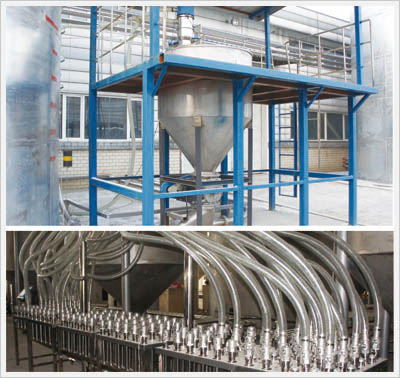
The system was completed and put into work in
January and still works well since then. It has realized the primal planning
target, which is to meet clients’ requirements by greatly saving cost of labor,
material, and energy, etc. and improving production efficiency. Some other
clients came to visit the system after it was installed. They highly approved
of such a way of operation and had signed purchase orders with us several days
ago. This case not only shows that Shini keeps self-disciplined and pursuing
self breakthrough on technology but also reveals that Shini will win
recognition on brand from more clients’.
Experience Sharing
If you want to read other articles, back to2013 Quarter 3 Issue 16.