Special Reports
2015 Quarter 1 Issue 22
Mold Sweat Dehumidifier Upgrade
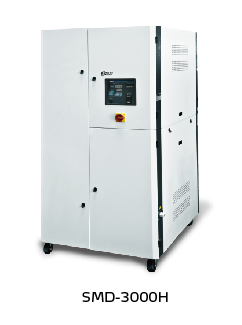
In order to have low dew-point and drying temperature air from Shini mold sweat dehumidifier as well as to adopt smaller mold dehumidifier in same working conditions, higher market competitiveness, we decide to improve the mold sweat dehumidifier.
The newly designed mold sweat dehumidifier SMD features the structure as following: air-return filter adopts plate filter that has advantages of filtering area enlargement and low-resistance ventilation. The air-return cooler changes into one input- one output and multi-branch hoses design, the special air collective cover makes the processing air evenly dispersed on the air-return cooler which improve the heat-exchange efficiency. The low-noise blower can improve the workshop’s environment. Upper and lower covers of the honeycomb integrated with special diffusing structure to ensure moisture sufficient absorption and rotor regeneration which improve the dehumidifying efficiency of the rotor. Cooler is added at the dehumidifying air outlet, which lowers the air temperature, and makes mold free from condensation. Air temperature is controlled by regulating valve for reasonable energy utilization. When the condensing water condensed air from the return air cooler and the water reaches the highest level, water auto-discharging function starts and water pump will start to discharge the condensing water out of the machine.
New mold sweat dehumidifier compared with the old model: firstly, largely improved the dehumidifying performance. Dew-point temperature of the open system can reach down to -15℃; secondly, minimum dry-bulb temperature of drying air can reach down to 16℃, which lowers the temperature difference of mold surface and makes uneasy condensation on it. Thirdly, it possessed the water auto-discharging function.
Dehumidifying property improvement of the new mold sweat dehumidifier means the same model can be used in larger injection molding system to ensure production efficiency and lower production costs. Under reasonable configuration, it prevents the mold from condensation which improves the quality of the plastics (specially the PET) and preforms.
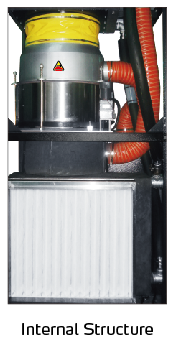
Special Reports
- The Preview of Shini Auxiliary Equipment on Chinaplas2015 Show
- Teflon Coating Applied in SGB
- sLink Protocol Solution
- Shini Robot Introduction
- Hot runner introduction
- Shini Japan
If you want to read other articles, back to2015 Quarter 1 Issue 22.