Special Reports
The PET Crystallizer SCR Improvement
PET,
with its scientific name polyethylene terephthalate, is also called
Dacron, polyester. Featuring excellent resistance of gases, resistance to
pressure, shock resistance, transparency and surface gloss, it is widely used in
food containers with traits of odorlessness fragrance
conserve, the safety of the food hygiene, beautiful shape and easily-forming.
It has density of 1.4kg/L,
melting temperature of 245℃,and molding temperature between 290℃ and 315℃. Its grain bulk
density fluctuates between 0.8 to 0.85kg/L,
sheet bulk density between 0.38 to 0.4kg/L.
PET mainly employed to produce
synthetic fiber, PET bottle and thin sheet. With the development of economy in
recent years, people’s awareness of environmental protection is under
enhancement. Thus PET sheet, as a kind of packaging material shows the
favorable development potential as the alternative to replace
difficult-recyclable PVC packing material.
There’re various
kinds of PET. When non-crystallized PET contacts with high temperature, it
would conglutinate. Crystallize PET can prevent material from conglutinating in
high-temperature drying, which usually ways of mixing and uses air flow to make
PET boiling in the process.
The function of crystallizing is to
crystallize PET and increases its melting temperature. It prevents PET from lumping
at the end of heating process. The non-crystallize PET is usually completed by
crystallizer with crystallizing temperature at 120℃~160℃.
The heating time is 1~2hr, the pre-crystallization process isn’t finished until
PET lost the transparency. PET is heated at even higher temperature after crystallizing
process to get rid of the residual moisture. For example, at drying temperature
of160℃, the
moisture contained in PET would below 0.05% after 4~6 hours rested in the
dehumidifying dryer. It helps to avoid PET hydrolysis at high temperature which
may lead to molecular weight and the viscosity drops down rapidly in extrusion
granulating process afterwards.
Shini PET
crystallizer standard equipped with the pre-heating function and constant-speed
mixing device which could effectively process crystallizing towards non-crystallized
PET materials. It avoids conglutinating in high temperature and improves PET
product’s quality.
In order to enhance
the performance of PET crystallizer, ensure machine’s operation as well as
machine’s convenient maintenance. We improved the structure of mixing
components for the PET crystallizer as below:
The gear motor
changed to mixing specialized gear motor with strengthened bearing at
output-shaft end. This strengthened bearing not only can bear even much radial
load as well as axial load but also can compensate the angle deviation in some
degree, which especially good for long mixing shaft application. Compared with
previous gear motor, it can bear much more load and with safer coefficient
which ensures steady and reliable mixing components.
Remove the middle bracket and bearing of barrel mixing components. It not only simplifies the processing technique and the assembly procedure, but also lowers the wearing of mixing internal components and makes convenient maintenance afterwards as well.
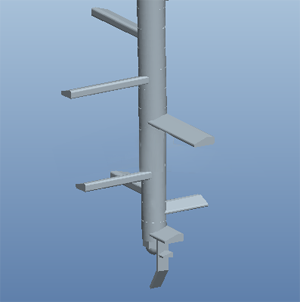
As to prevent the material at hopper bottom from bridge-breaking, the mixing blade at bottom also be lengthened which ensures material discharging smoothly.
The modified PET crystallizers are in stable, safe and reliable operation, and machine’s maintenance is more convenient afterwards. All of these can satisfy the quality, safety and maintenance requirements from the customer, which established the solid foundation of the machine for future clients.
Special Reports
- Industrial Water Chiller COP Introduction & the China Standard
- RS485 Communication Interface Applied in Mould Temperature Controller
- Working Principle and Practical Implication of Cyclone Separator
- Conveying Control Differences between SHR-U-(E) S Applied on SGB and Other Machine
- Application of SICH-U Insulated Collective Hopper
- In What Circumstance to Use Hot-runner
- About Shini Europe
If you want to read other articles, back to2015 Quarter 2 Issue 23.